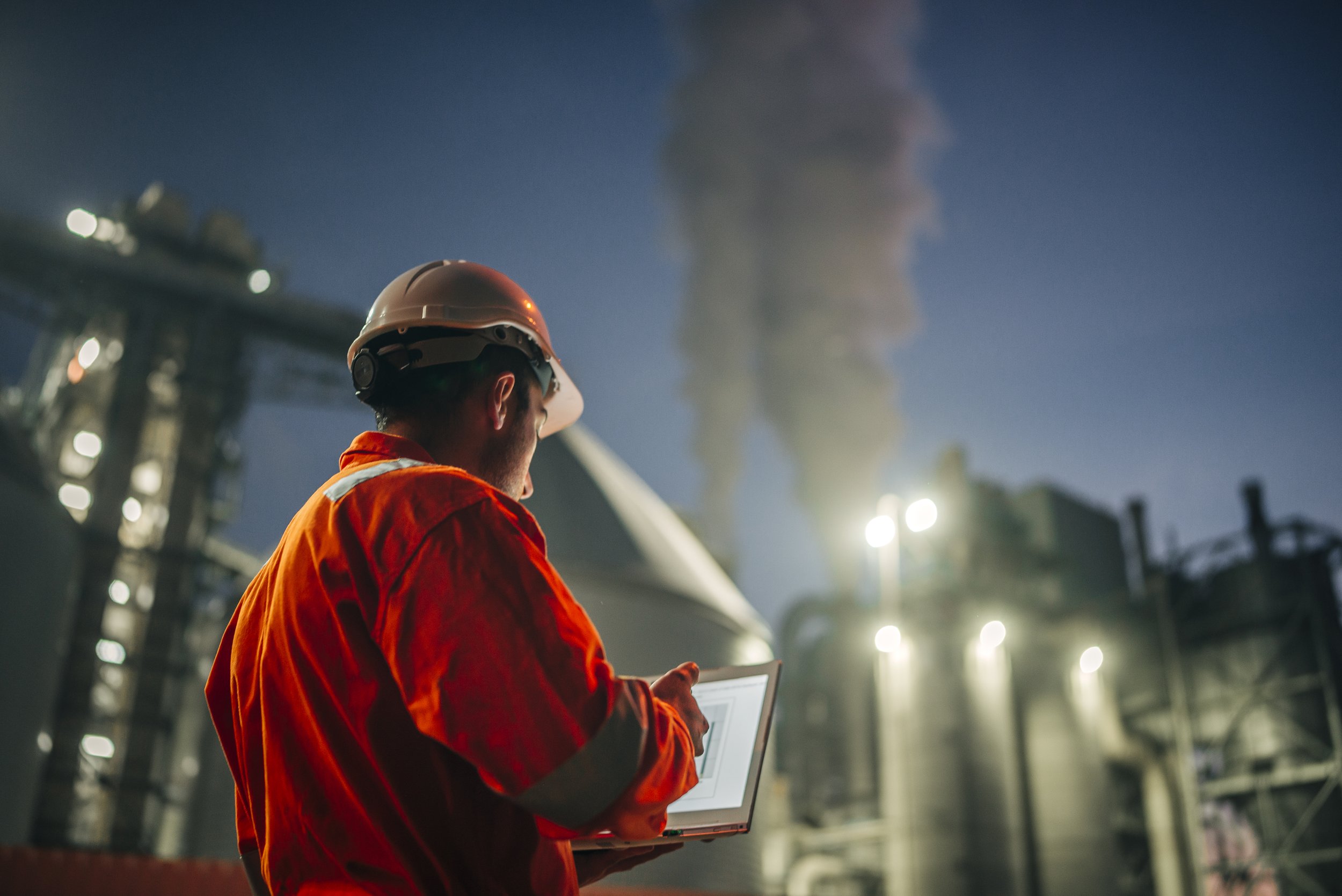
FASForm: Next Generation Fuel-Discovery Technology
We turn coal into fuel.
A new energy recovery category, Solid Carbon Fractionation.
This new process deconstructs coal by extracting volatiles, moisture, and contaminants. Resulting in the delivery of hydrogen, methane, naphtha, diesel, aviation fuel, and FASCarbon™, a clean coal.
With our technology, coal will be a source of multiple energy products, producing cheaper power, and ‘cleaning up’ every aspect of coal.
01.
02.
03.
04.
Global Growth
Patents on 5 Continents.
9 countries including the U.S. and Canada.
Covers 85% of the global coal market.
Impacts over 3.3 billion people.
01.
Global Growth
Patents on 5 Continents.
9 countries including the U.S. and Canada.
Covers 85% of the global coal market.
Impacts over 3.3 billion people.
Coal
The most abundant, affordable, available natural energy resource.
Used to meet nearly 40% of electricity demands globally.
A FASForm unit will process 7,500 tons of coal per day, or roughly 2.7 million tons annually per facility.
The U.S.’ coal production is 540 million tons annually. Each facility will process 0.5% of the United States’ annual coal production.
02.
Coal
The most abundant, affordable, available natural energy resource.
Used to meet nearly 40% of electricity demands globally.
Our facilities will process 7,500 tons of coal per day, or roughly 2.7 million tons annually per facility.
The U.S.’ coal production is 540M tn/year. Each facility will process 0.5% of the United States’ annual coal production.
FASForm™
FASForm is a validated and patented technology that applies a continuous feed process using thermal cracking and distillation of coal.
First technology that “fractionates” a solid hydrocarbon into liquid fuels and a clean, low-sulfur technical carbon coke - known as FASCarbon™.
FASForm technology eliminates coal combustion globally with zero waste and low emissions.
03.
Solid Carbon Fractionation
SCF is a validated and patented technology that applies a continuous feed process using thermal cracking and distillation of coal.
First technology that “fractionates” a solid hydrocarbon into liquid fuels and a clean, low sulfur coal - known as FASCarbon™.
Our technology eliminates coal combustion globally with zero waste and low emissions.
Outcome
Produces 2.3 barrels of liquid fuels from each ton of coal processed.
Produces FASCarbon™, a virtually sulfur-free coal. Functions as a replacement carbon for steel manufacturing and coal-fired plants that burns hotter, cleaner, and with lower emissions.
04.
Outcome
Produces 2.3 barrels of liquid fuels from each ton of coal processed.
Our closed-loop process produces over 20 million standard cubic feet per day (mmscfd) of hydrogen used to power our facility.
Makes Frontieras the first plant powered by hydrogen in the United States.
Produces FASCarbon™, our virtually sulfur-free coal… a replacement carbon for steel manufacturing and coal-fired plants that burns hotter, cleaner, and with lower emissions.
-
FASForm™ Competitive Advantages:
• FASForm™ is a simple process that capitalizes on coal, a more reliable and price stable feedstock than natural gas, with low processing and capital costs, to generate liquid transportation fuel prices at costs cheaper than any other known technology or recovery method.
• Profitability is significant when crude prices are as low as $15/barrel and since OPEX costs are independent of crude prices, profit grows significantly as crude prices rise.
• Crude oil price and the resultant global market for transportation fuels is the only significant factor affecting profitability.
• FASForm™ is only moderately sensitive to capital cost and has low sensitivity to feed stock price.
• FASForm™ is a low emissions solution that provides net environmental improvement to the full energy cycle.
• FASForm™ is a rational solution to extend the life of the existing generation asset base to meet greenhouse gas reduction initiatives in industrialized and developing countries.
FASForm Technology:
• FASForm is a thermal cracking process operating in a reducing atmosphere (no combustion or oxidation) at slightly positive pressure and moderate temperature. FASForm is much simpler, less expensive, and less polluting than conventional gasification and liquefaction technologies (CTL). It does not require makeup water and does not produce CO2. FASForm is also more proven and much less expensive than attempted unsuccessful carbon sequestration and capture/re-use technologies for an equivalent reduction in CO2.
• The conversion of coal to synthetic crude has been proven since the 1930s. The FASForm innovations are the continuous, in-process fractionation of the extracted hydrocarbons into separate liquid fuel streams. These innovations are grounded in straightforward refinery and fluidized-bed reactor engineering and FAS has conducted pre-commercialization development testing, which has validated the process innovation and affirmed commercial application being witnessed and reported by a reputable third-party engineering firm.
• Extensive Patents for both Method and Apparatus have been granted in the 9 largest coal producing nations: the United States, Canada, Australia, India, Indonesia, South Africa, China, Russia, and Germany. Disclosures have been made in another 139 countries under the International Patent Cooperation treaty.
• FASForm™ plants operate continuously 24/7 matching the operating reliabilities of the product end users. The continuous generation of segregated products is a unique and disruptive change to existing, proven technology for liquids recovery from coal and lignite.
-
Thermal Markets:
• FASCarbon functions as a co-feed or replacement carbon for thermal markets.
• FASCarbon is demoisturized, and the absence of moisture alleviates the need for volatiles, yielding 14,000 BTU/LB.
• At less than 1% sulfur, the environmental benefits of FASCarbon are substantial for thermal markets.
Petcoke Markets:
• With a lower sulfur and moisture content, FASCarbon’s price, heating value, and efficiency is highly competitive in ptetcoke markets.
• FASCarbon is free of all heavy metals.
• FASCarbon’s clean properties make it a solution for environmental requirements in petcoke markets.
Steel-Coke Markets:
• FASCarbon™ is nearly sulfur-free and burns as clean as natural gas.
• FASCarbon can be used as a replacement carbon for steel manufacturing, it allows US steel makers to hit significantly higher production volumes while maintaining sulfur-emission compliance. Iron-Ore steel manufacturing requires the injection of carbon, a constituent of steel.
Other Environmental Benefits of FASCarbon:
• The Environmental Protection Agency heavily regulates sulfur emissions (SOX). SOX emissions are a threat to human, animal, and plant life. Hence, many sectors of energy and manufacturing are currently and will continue to be heavily monitored and constrained by sulfur emissions thresholds.
• Treated fuel gas streams composed of Hydrogen and Methane, and other rich gases will power our facilities. Frontieras’ facilities will be the first and likely one of the largest Hydrogen powered in North America.
• Segregated Liquid streams: Naphtha (chemical feed stock or gasoline intermediate - 25% of total), Kerosene (jet fuel intermediate - 30% of total) and Diesel (40% of total) requiring only simple hydro-treating to produce Jet Fuel and Ultra-Low Sulfur Diesel (ULSD).
• FASCarbon: a clean high-energy solid fuel that can replace non-US EPA compliant raw coal and lignite in power and industrial plants lowering generation costs while meeting or exceeding proposed US EPA emissions rules.